Pon.Bike Factory in Kėdainiai
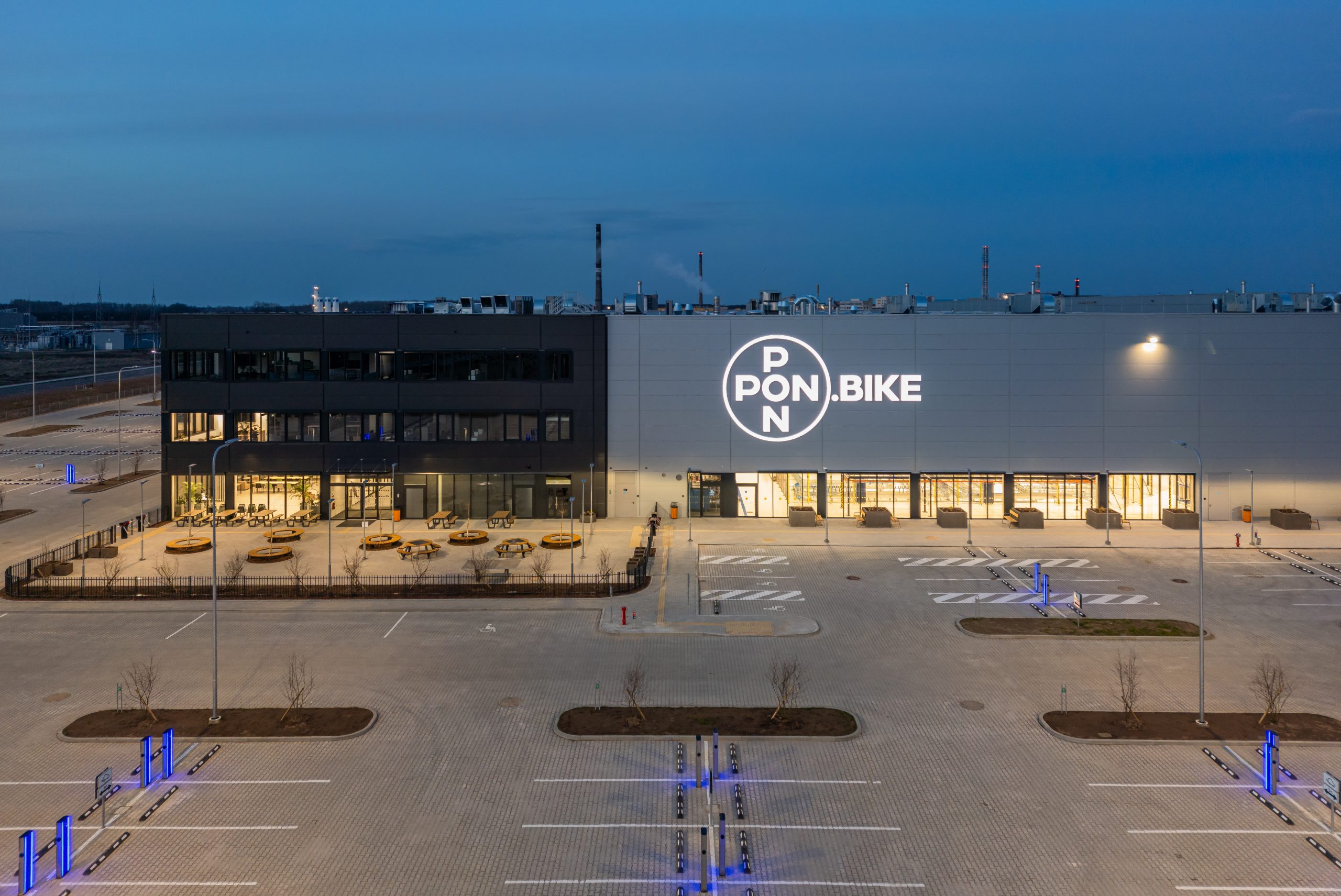
- Location Kėdainiai, Lithuania
- Type Industrial
- Size 39 650 m2
- Year 2022-2024
- Status Completed
- Client UAB Pon Bike Lithuania
- Images Gerda Ramonė
- Project lead Julius Lapinskas
- Authors Gabrielė Liucija Ošikaitė, Julius Lapinskas, Jevgenij Kuzimin
Pon.Bike - the world’s largest bike family entrusted us to design their new manufacturing facility in Kėdainiai FEZ. The factory was designed and built utilizing modern technologies to meet the highest sustainability and clean production standards. Bicycles for a wide range of brands including Gazelle, Kalkhoff, Focus, Swapfiets and Urban Arrow are made there. It is a 40.000 square meters workplace designed for 570 people which includes bicycle assembly lines, painting facilities, a warehouse and a three-story administrative premises.
This project exemplifies our approach to industrial architecture: combining functionality, sustainability, and aesthetics to create a space that serves the client, employees needs and the environment.
-
- m/tons
-
Project regarded by the state as a large investment project, 2024
-
First BREEAM Excellent certification for Industrial buildings in Baltics, 2025
-
FM Global Highly Protected Risk (HPR), 2024
Responsible development for E-bike manufacturing
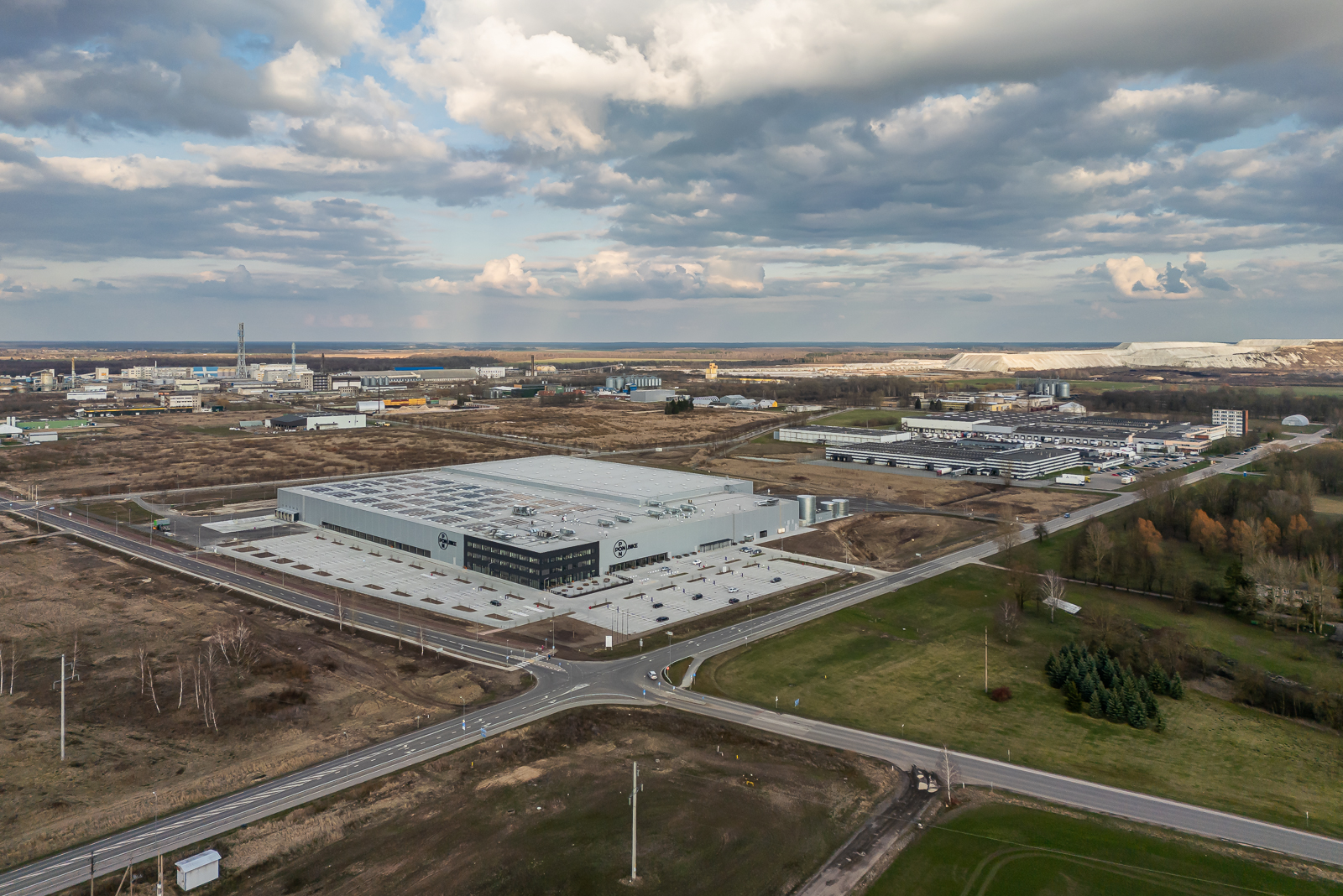
Pon.Bike bicycle factory is one of our biggest and most challenging projects to date. The bar was raised very high by the Clients design task and high-standard certification expectations. This pushed us to overcome the challenges along the way and to create a modern, sustainable and human-centered factory.
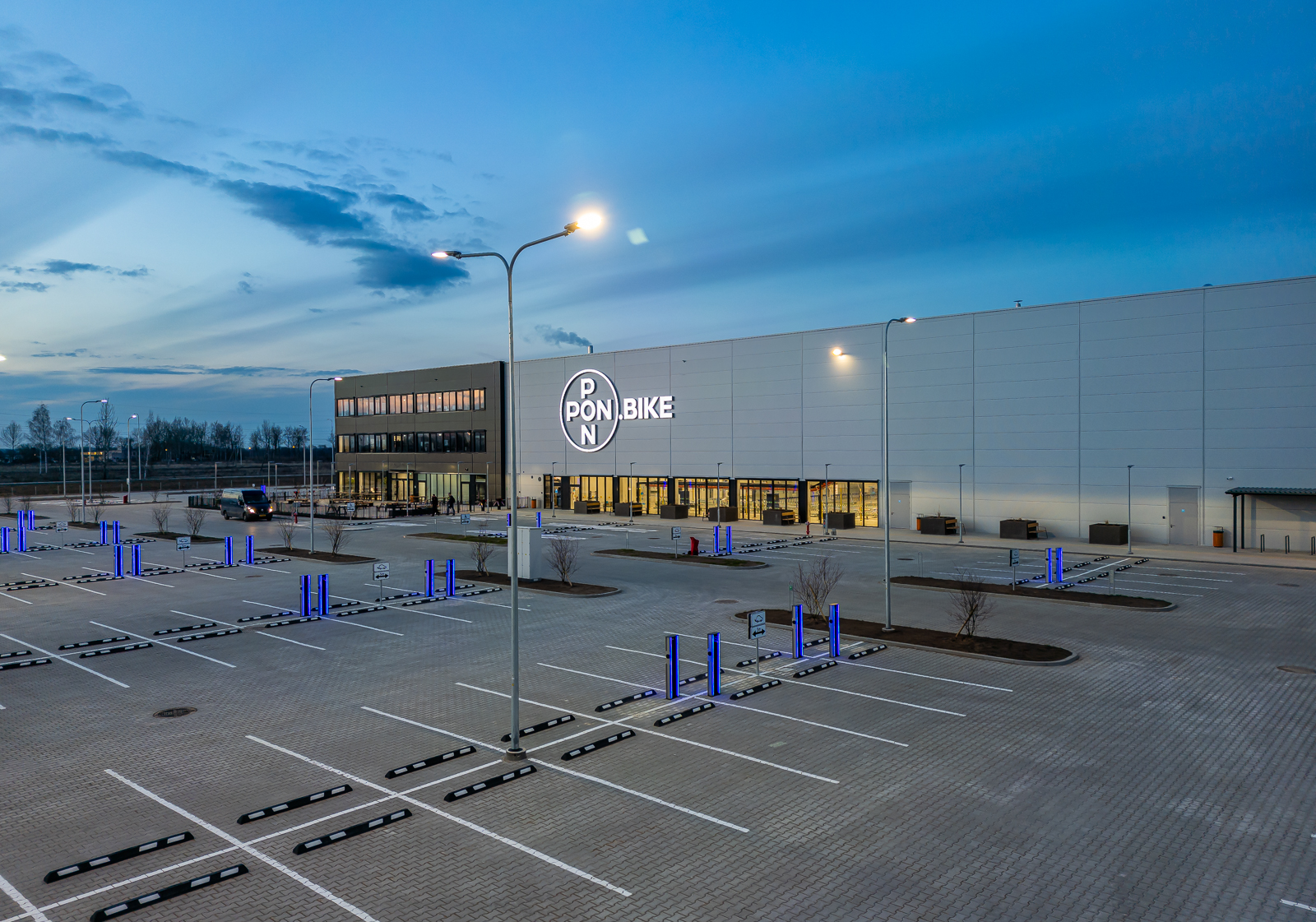
The real challenge of this project was designing up to the FM Global and BREEAM standards. The requirements were very high and therefore various solutions were implemented. This building is one of the few in Lithuania with FM Global certification and the first Industrial building in the Baltic states with BREEAM Excellent certificate.
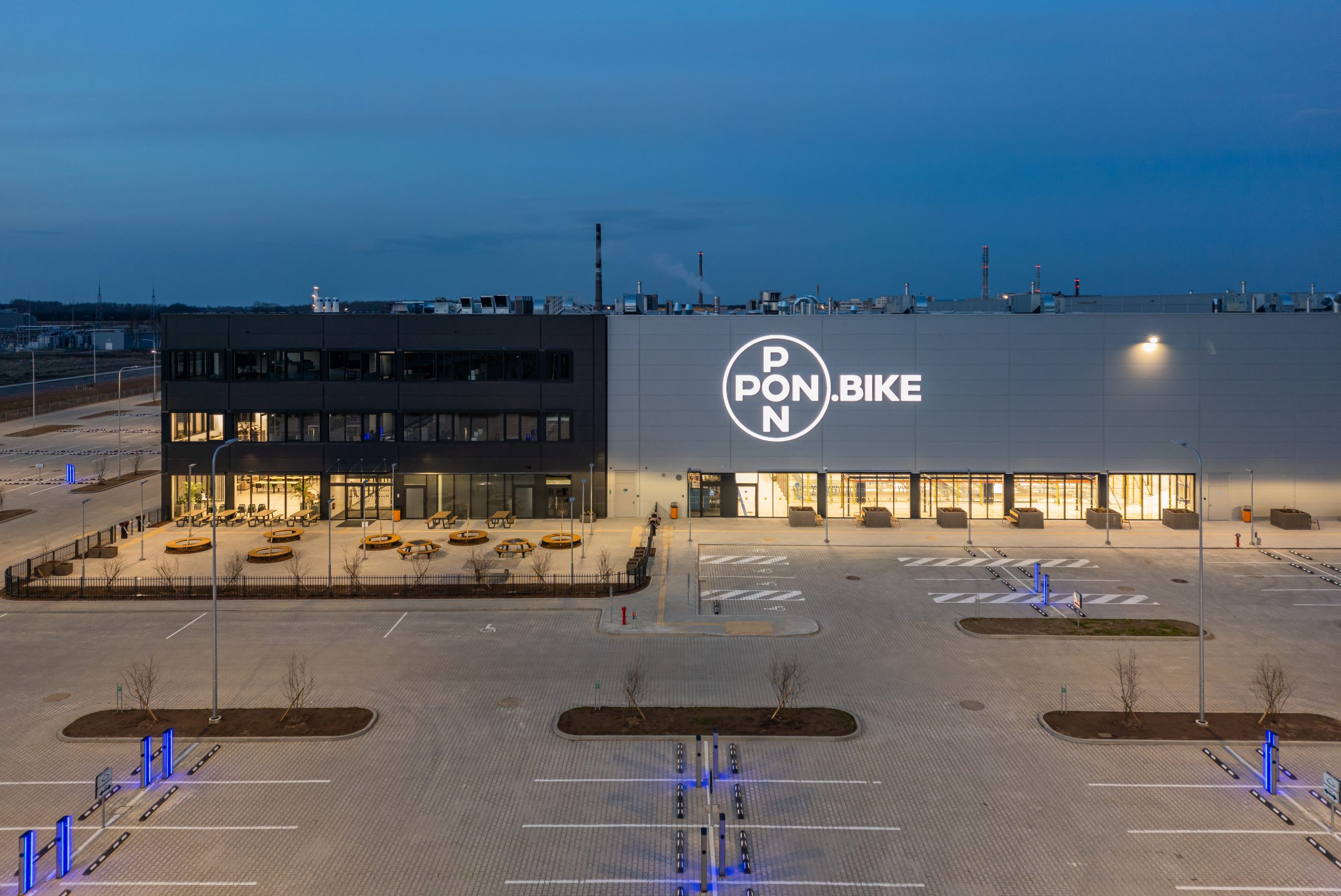
To satisfy FM Global requirements the project was repeatedly reviewed by the certified consultants and design solutions were implemented in the structural part, sprinkler design and outdoor and indoor rainwater projects. As for BREEAM we had amazing consultants that formed us a design task to be implemented in the project to achieve the “Excellent” rating.
Project stages
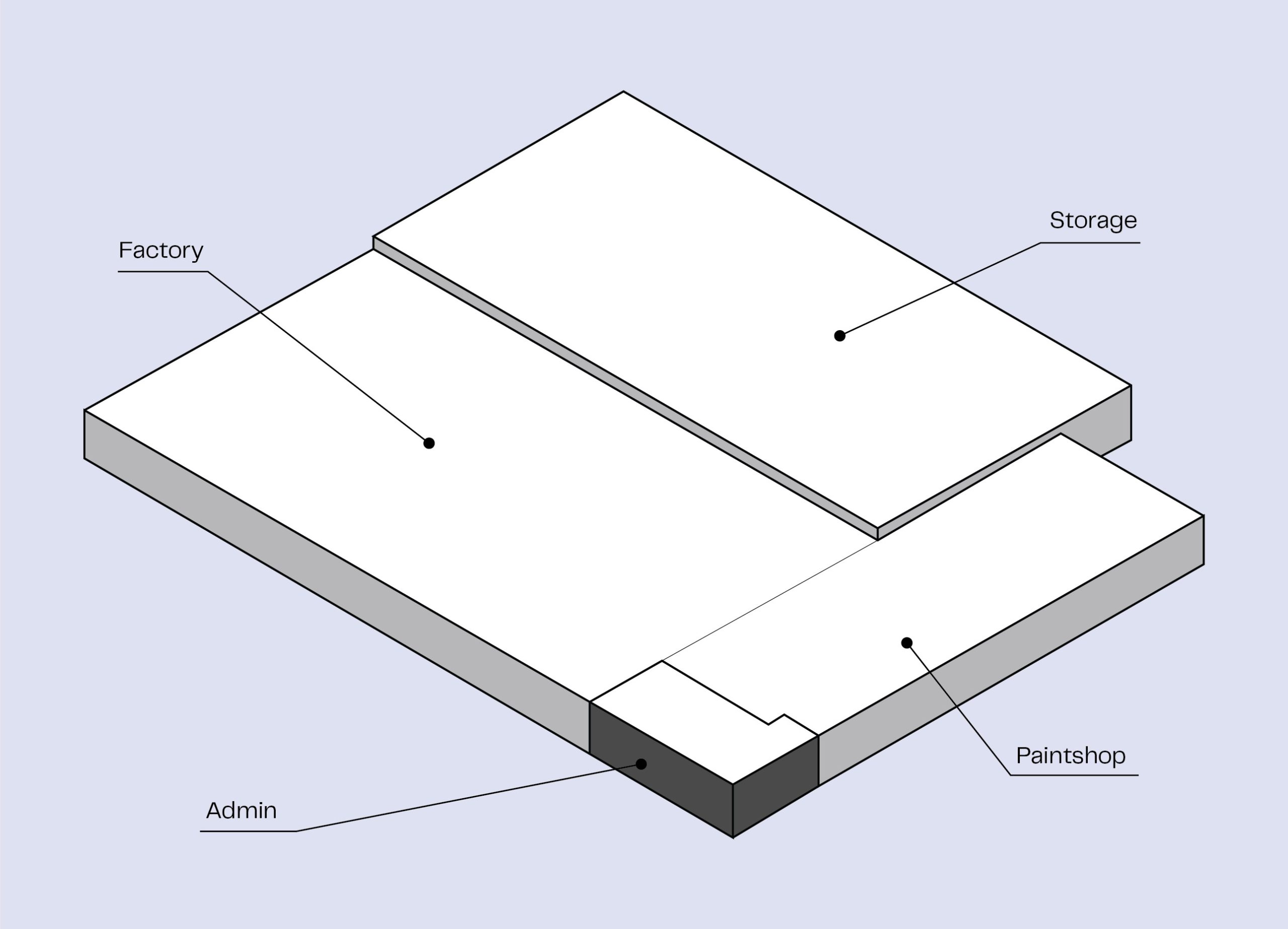
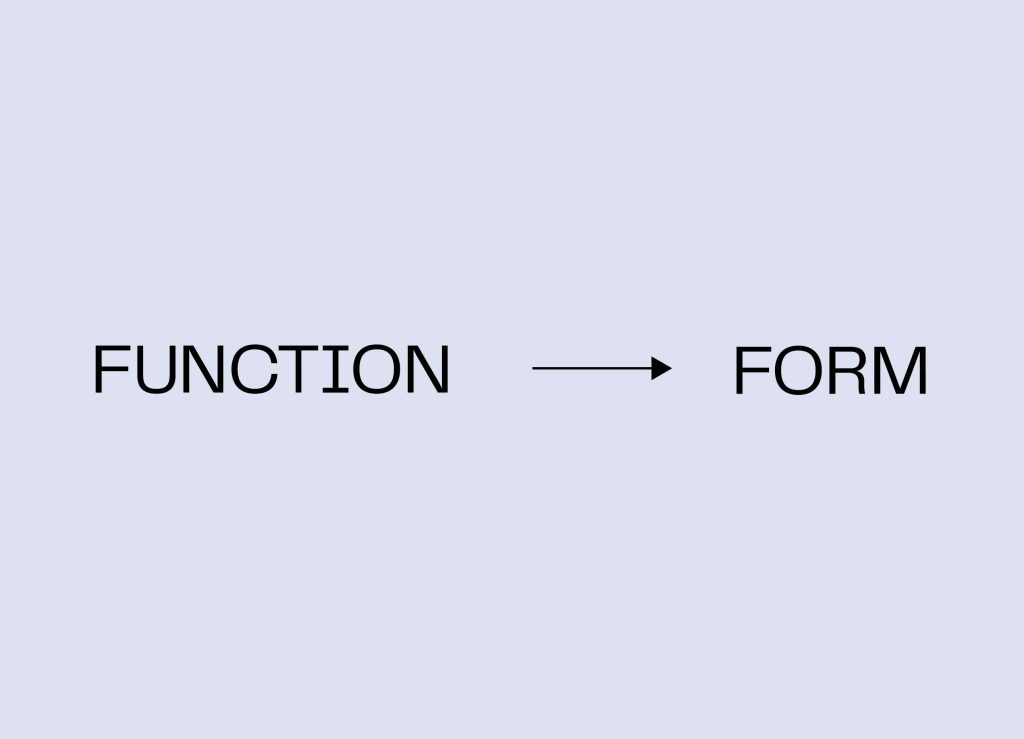
As the saying goes – form follows function. The main aim of the project was to create the most efficient layout using simple but high–quality means. The building is comprised of 4 functional parts that are co-joined together. The 4 volumes have different height to appropriate the neccesary functions.
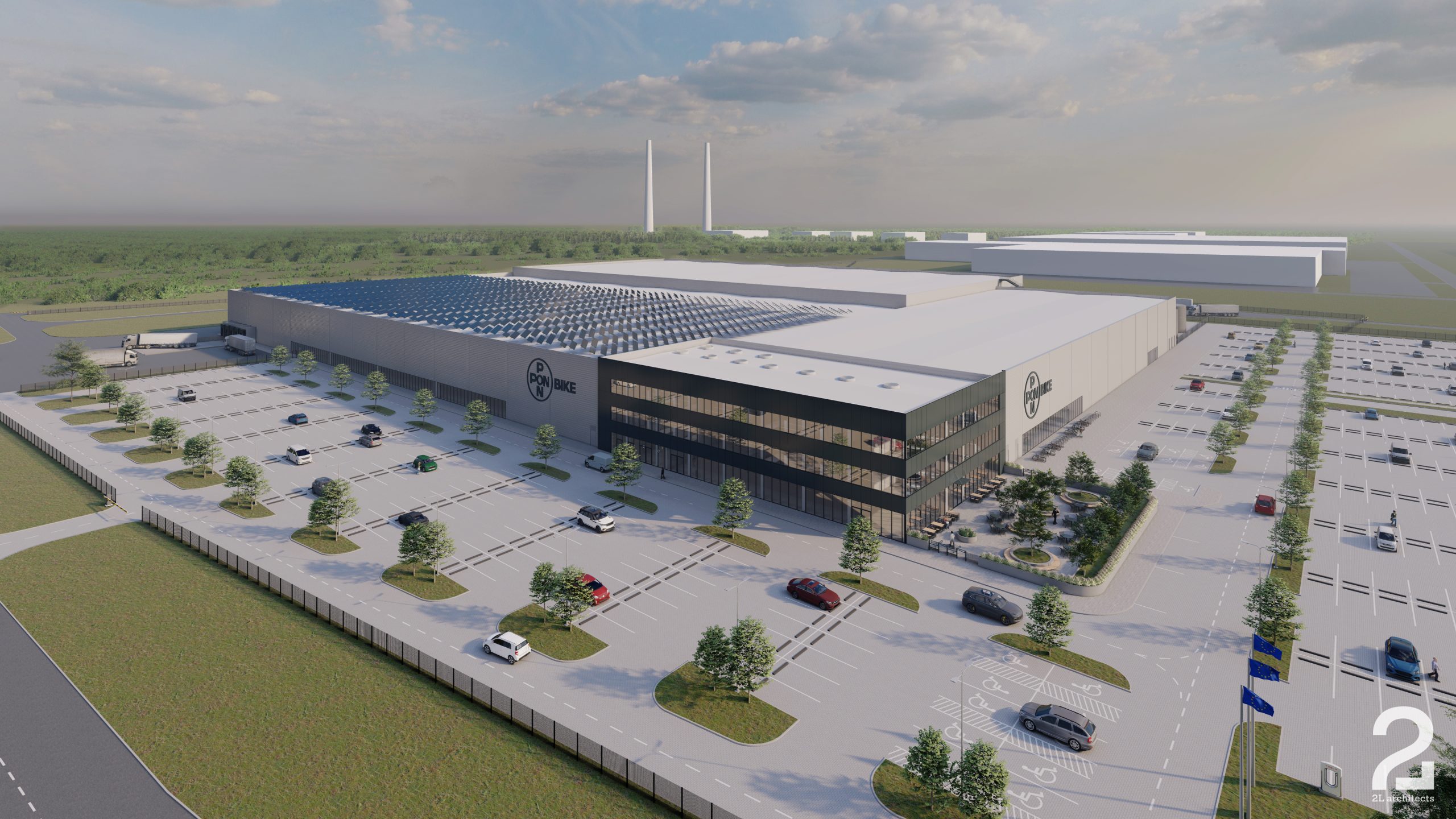
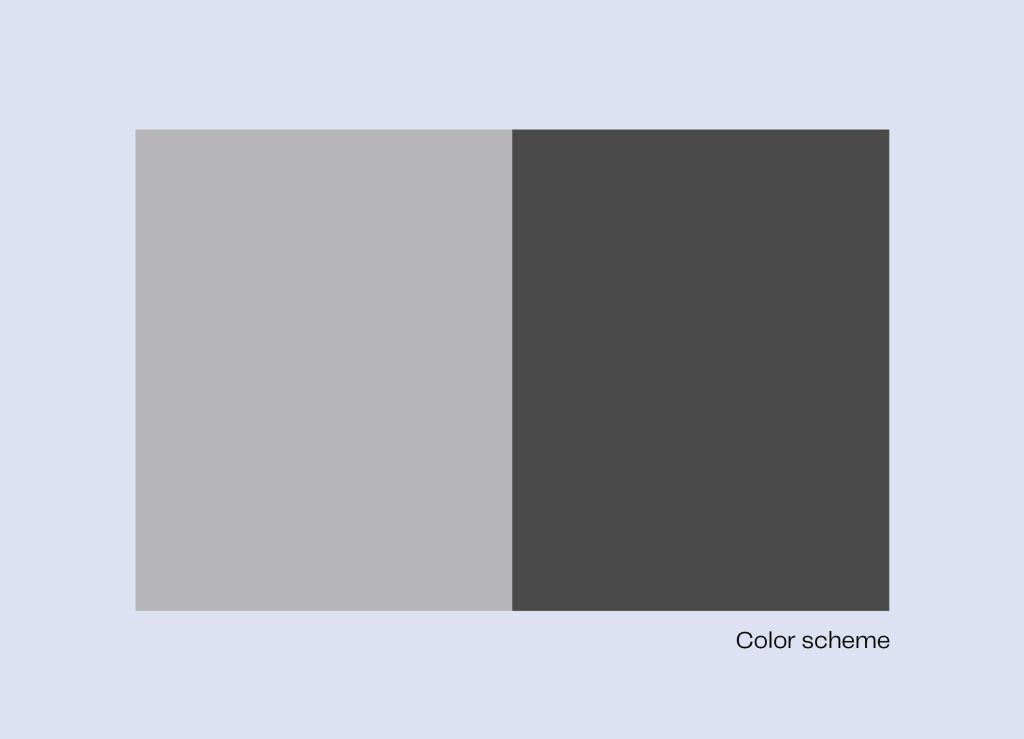
The main aim of the project was to always keep the end-user in mind. Therefore, an atrium with circle skylights (bike wheel) was designed inside the administrative volume to create the feeling of connection throughout all of the floors and all of the employees. As for the exterior, simple but high quality materials and complimenting colors were used.
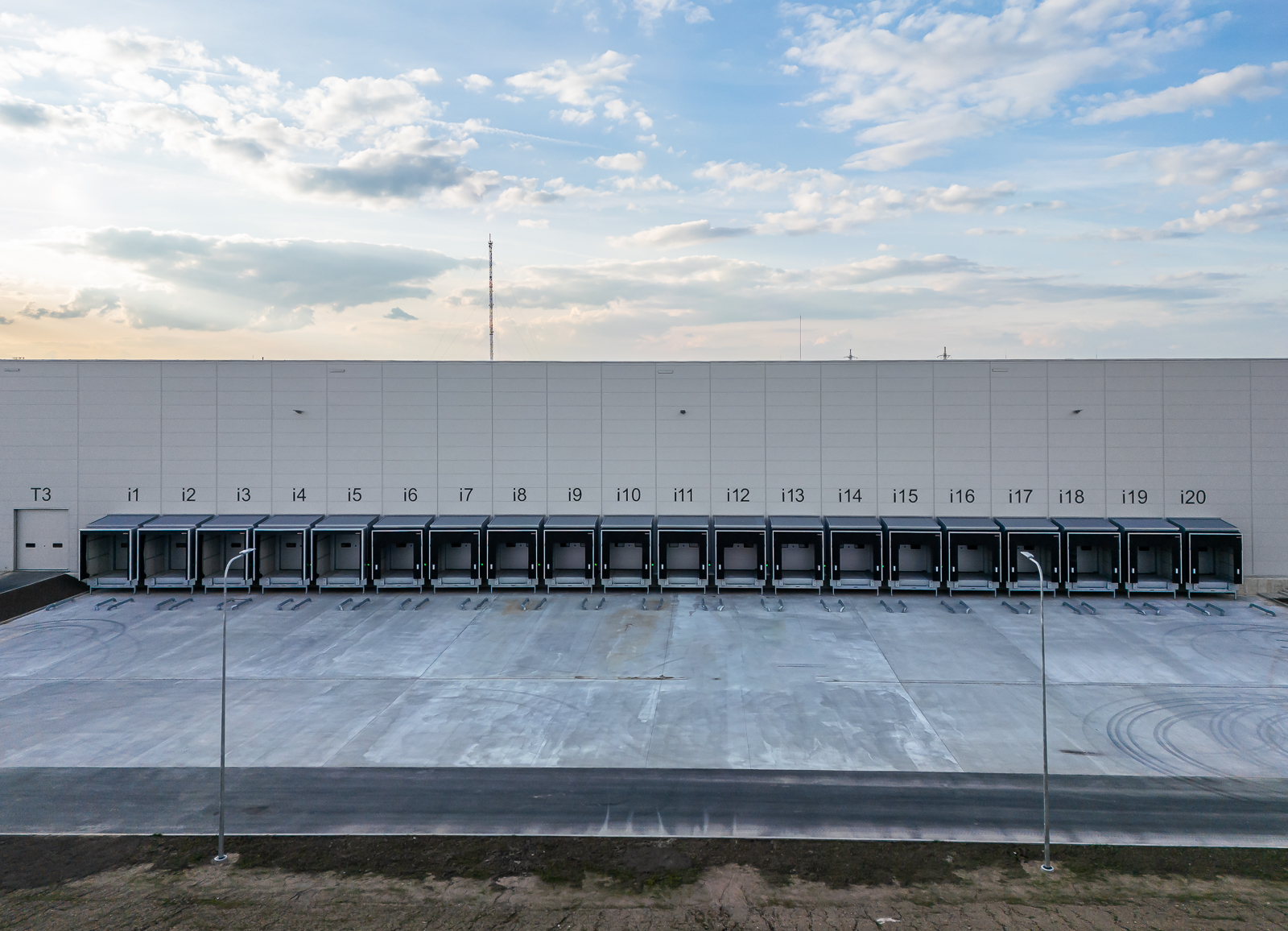
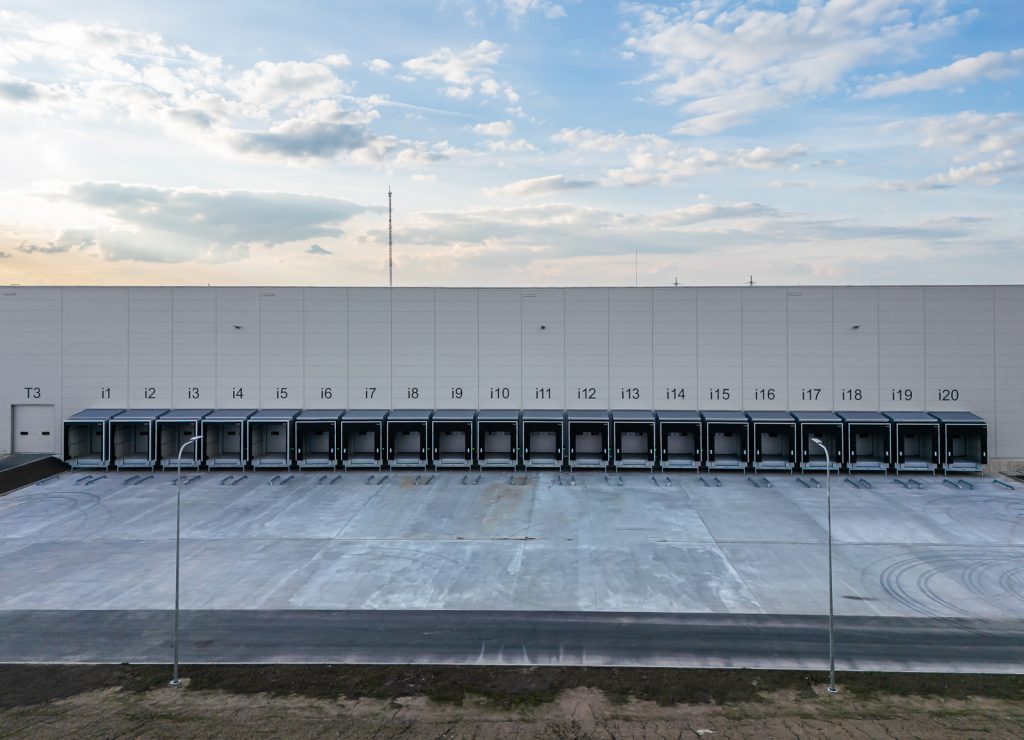
Engineering here was crucial. The complexity of paintshop technology was a great challenge to overcome. Only with the help of BIM and clash detection did we manage to coordinate the very complex technological paintshop ventilation system and other engineering systems of the building. Not to mention, the enormous electricity needs of the building. Therefore, a 800 kVp solar power plant was designed on the roof to accomodate the electrical building needs.
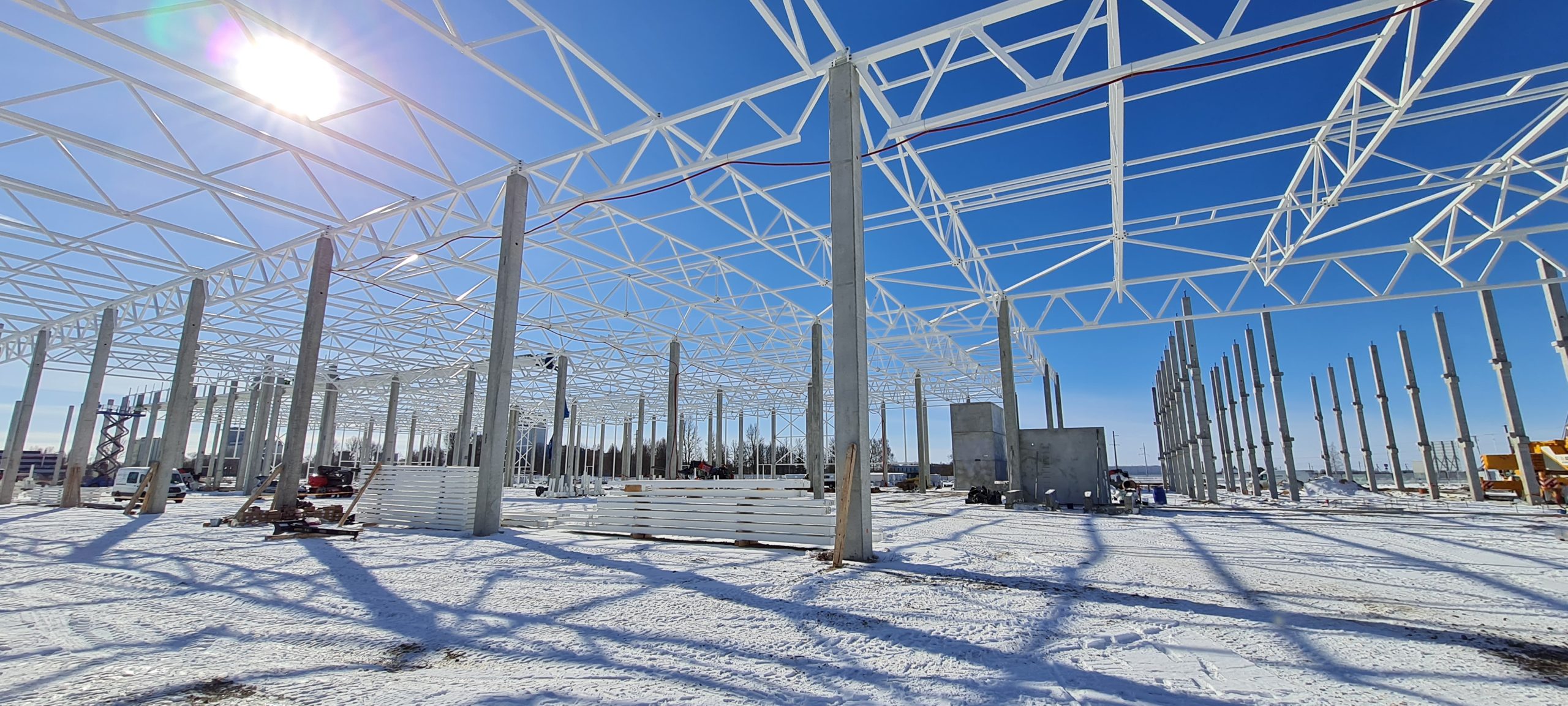
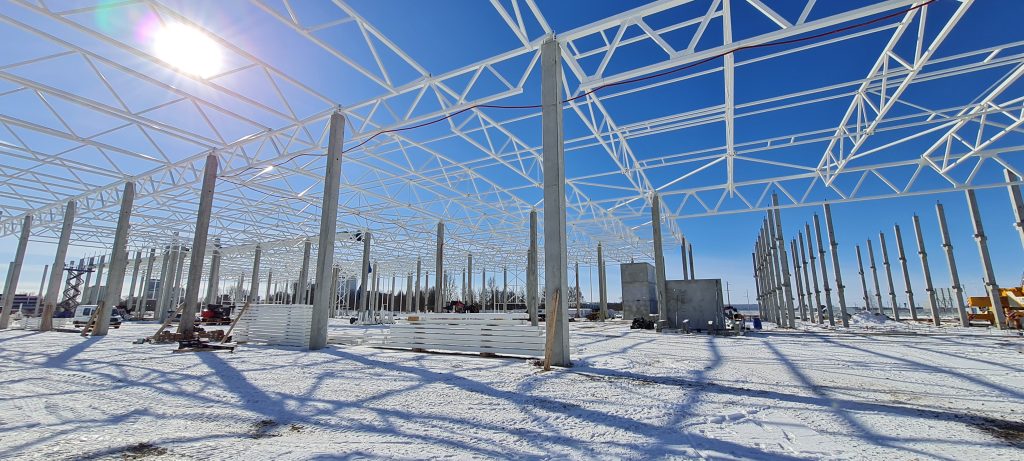
The factory was built extremely fast by using modern technologies such as Dalux and BIM for productive building processes. By using 3D modeling software the building drawings were made in the most efficient way minimising the amount of mistakes. By combining all of the engineering models we were able to catch clashes between project parts.